SUPPLY CHAIN: CERTIFYING THE CONTROL SYSTEMS
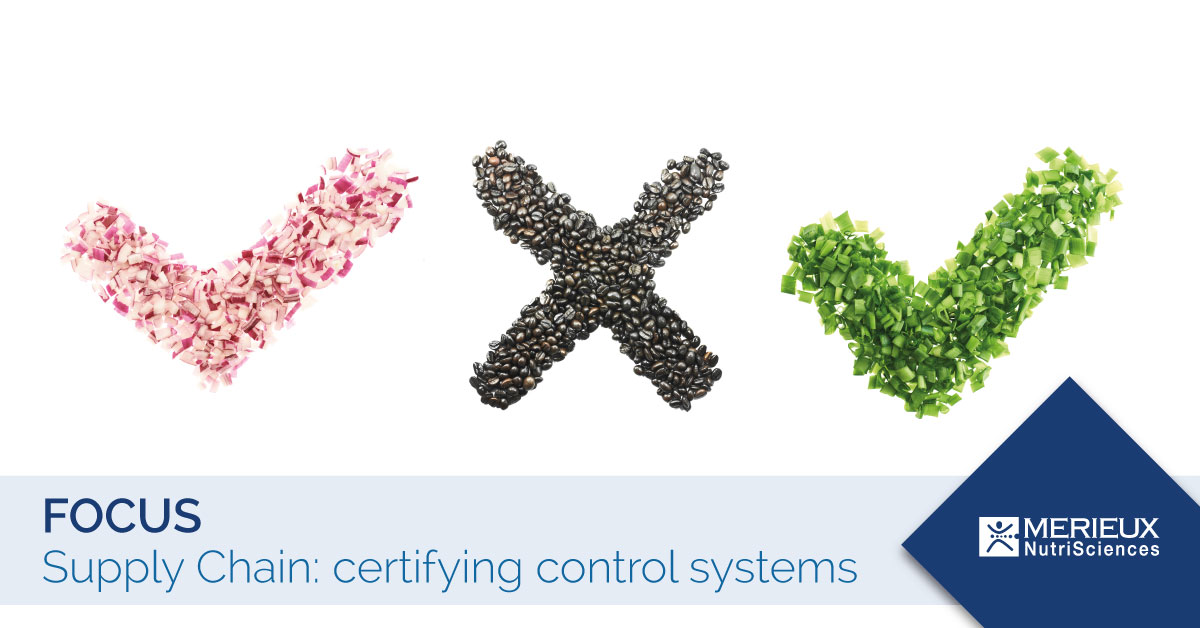
Certifying a control system of product suppliers means focusing the attention on the adequacy and effectiveness of the verification and management procedures of both suppliers and their products.
Preamble
Before addressing the elements that characterize the certification of a control system, some cornerstones of this process shall be listed.
Distributors, especially those who manage the Private Label, know how important it is to:
- have reliable suppliers;
- uniquely define the requirements of each product;
- provide a compliant labeling service;
- establish the compliance checks.
Before being measured over time, the reliability of suppliers must be considered in the selection phase through audits and the assessment of documentary requirements. Product requirements are composed of specifications agreed and signed between the parties and they can involve various aspects such as the intrinsic characteristics of the products (including the origin of raw materials) or the control methods to be activated in the process and final stages. The adequacy of the labeling must take into account legal constraints and communication needs while product compliance, or the confirmation of compliance with the requirements, is usually implemented through a laboratory analysis service.
The supplier management system
The structuring of a system that allows the above to be properly managed means establishing a policy with clear goals, identifying and making available the adequate resources, implementing the necessary operational and control activities and applying effectiveness measurement tools and periodic review activities. At this point, the priority is to effectively manage the control activity based on four fundamental pillars:
- have suppliers audited;
- draft specifications;
- verify labeling compliance;
- perform the analytical control of the product.
The desired goal is generally the placing and consequent presence of a reference on the market which is why the four points listed above cannot be neglected, to avoid loss of control, with repercussions on the image not only of the product, but also of the whole brand.
The certification of the control system
This is where the certification of the control system plays its role. The aim is to ensure that, according to the principles of quality –“do it right the first time”– and that human and economic resources are well employed in a balanced relationship consistent with the goals and principles of precaution.
Certifying this system means voluntarily submitting it to the approval of a third party that assesses its consistency with respect to the policy and company targets, also measuring the level of application.
The certification of the control service has as its first objective the correct internal management of the areas responsible for product quality and communication and not, as you might think, the visibility of the application of the verification procedures towards the end customer. For this reason, the certification of the control system must be seen as an opportunity mainly aimed at improving internal management, such as to allow the distributor to apply its procedures with the utmost confidence.
Communicating to the final consumer that adequate and continuously verified quality control systems are applied, to increase purchase confidence is useful and advantageous only at the end of this process.