SUPPLY CHAIN: WHAT IT IS AND HOW TO SET IT UP IN THE BEST WAY
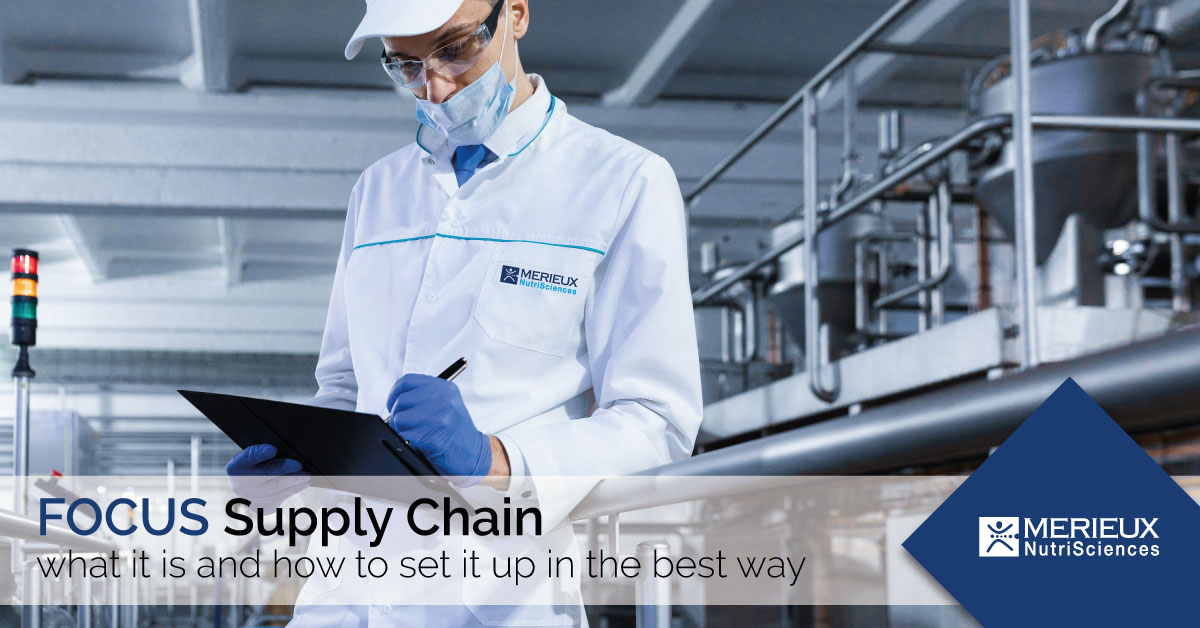
From risk analysis to the determination of control systems.
The Supply chain (commonly called Distribution chain) is a recurring definition and an
expression indicating the economic relationships stemming from transactions of goods and
services between customers and suppliers, in all economic sectors, subject to compliance
with expressed or implicit requirements.
The Supply chain could be defined as a bond between incoming and outgoing elements
managed and processed by various players that lead to the result or what is aimed at the
last user. From wheat to pasta, from essential oil to hand cream, from vegetable fiber to
clothing, the work of each entity involved in a given chain influences the quality of the final
result in a more or less significant way. Just like the rings of a chain.
The Supply chain is a continuously evolving entity that is determined by the rapid changes
of both conditions and contexts, which tends to the maximum efficiency of the processes
and the minimization of errors.
In this scenario, the control of the various links is decisive, and those who purchase goods
or services are forced to be increasingly attentive to the reliability of their suppliers.
If a handshake was enough to seal a relationship of trust between customer and supplier,
now it is useful only if –following careful control procedures– the ability of a partner to
satisfy the expected requirements can be attested in a sound and objective way.
Preparing and processing a supplier selection, qualification and control procedure is
simple; the guidelines on Quality Management Systems indicate with clear and often
standardized passages the criteria to follow and the tools to use: questionnaires,
certification requests, audits and anything else that may be needed.
However, what should be the starting point? What is the right approach to avoid focusing
too much on the checks, without first asking the reason why?
The line that unequivocally determines the selection and surveillance systems is the Risk
Assessment, the true beacon of all the actions they achieve on suppliers.
The Risk Assessment (or Hazard Analysis) is a process that derives from the Food sector and
which provides clear steps:
- supply chain mapping;
- evaluation of specifications and requirements of products or services, including intended uses;
- identification of potential hazards;
- identification of the severity and possibility of occurrence.
What would appear to be a classic HACCP approach is actually a system that can be
applied to any sector of transformation and service. The dangers are obviously identified
based on the context, which is why the necessary time and attention must be reserved.
A very simple and immediate system is to make a list of all the hypothetical events, without
discarding a priori what it believed to be unlikely; in fact, the assessment of the probability
of happening is the next step.
However, if this activity is carried out in an inappropriate manner, applying irrelevant
procedures and plans is the risk. In the worst case (the underestimation), a loss of control
might occur or we might find ourselves using unnecessary resources for performing
controls.
It goes without saying that in order to conduct a correct Risk Assessment, to identify the
dangers and weigh them properly, access to information is fundamental. This means being
aware of information regarding events such as non-conformities, recalls and sector-related
crises.
This is the reason why certain voluntary certification schemes such as the GFSI (Global
Food Safety Initiative) explicitly refer to the need to acquire valid updating and information
tools –for example on the issues of health and hygiene risks– or on the authenticity of the
products.
Only once the level of risk is determined, the most appropriate control systems can be
considered. From this point of view, the solutions and their combinations are manifold:
documentary requests, traceability checks, on-site or off-site audits, implementation of
tests and controls (including analytical ones), are among the most usual tools.
Among these, a very concrete and pragmatic method to check the efficiency and
proactivity of a supplier –in particular the product– can be testing him about the history,
controls and specifications of an item delivered and taken as a sample. From a batch of
products, request information on traceability, acceptance checks, process and final
checks, but also on system procedures, such as those relating to the human resources
used. Based on the time and validity of the response, the organization of the supplier and
its ability to ensure constant quality can be evaluated.
Therefore, this is no longer a general investigation that starts from the Quality
Management System, but a punctual and vertical verification that can go through all the
issues and aspects of interest.
This is just a small example of what the possibilities of control may be, bearing in mind that
there are no better systems than others in absolute terms, but only more appropriate
solutions.
As mentioned at the beginning the term "chain" is not random and recalls two very important
concepts: the solidity of each ring and their intersection. Only if these two aspects are guaranteed,
the tightness of the chain can be really trusted.